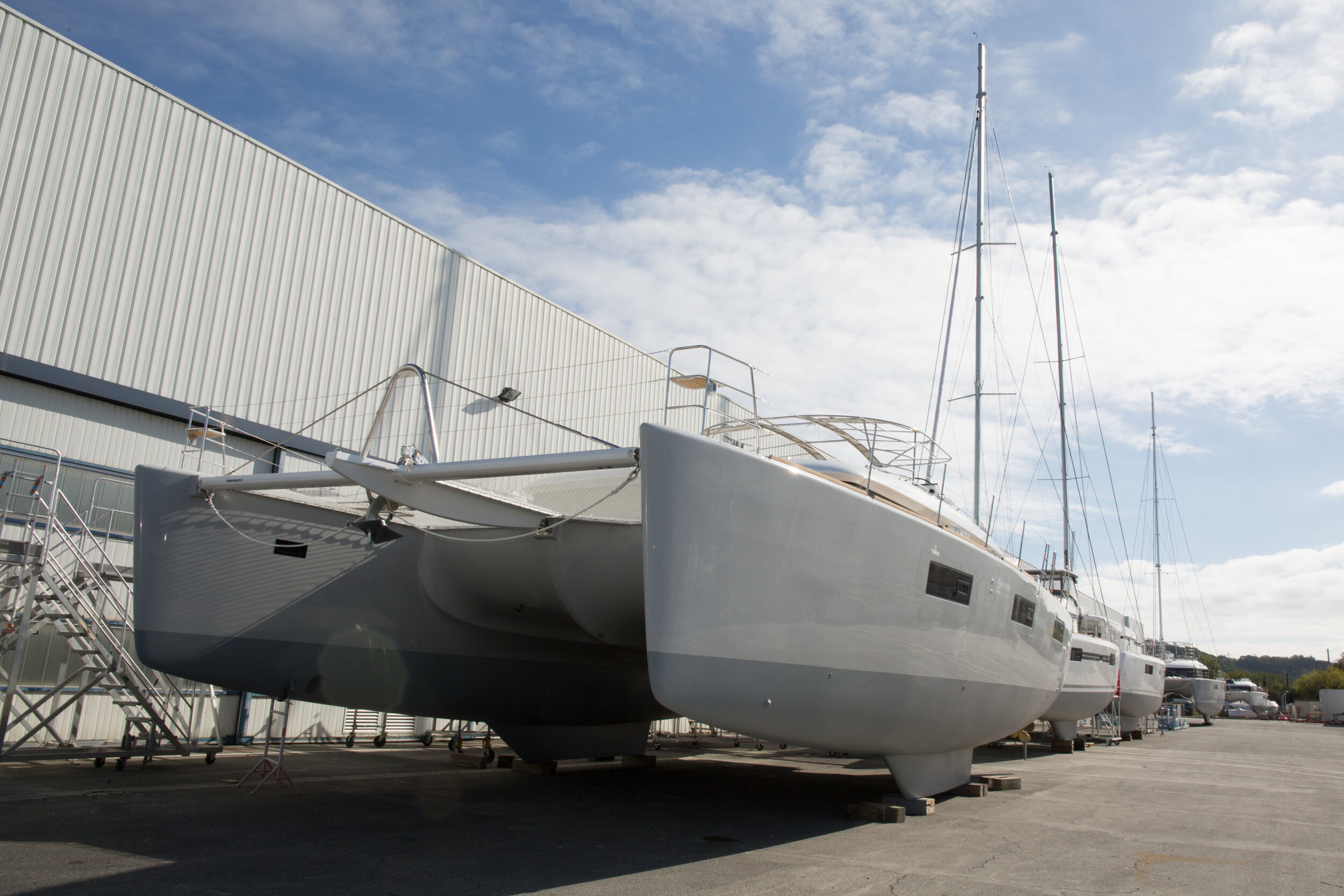
3D Core Kits
For lighter and faster boats.
We thermoform 3D core kits for climate conscious boat builders.
Traditionally, boat hulls have been produced by slicing up flat foam panels and fitting the sliced panels into the curved surfaces of the boat hull. This process results in many cavities in the foam core, which are afterwards filled with resin.
With 3D Core Kits, the foam panels are thermoformed to accurately fit the boat hull design. Leaving no cavities to be filled with resin. With less resin used, the weight of the boat is significantly reduced. And so is the carbon emission during production.
A 3D thermoformed Core Kit is the perfect choice for eco-minded boat builders who also aim for lighter and faster boats.
3 step process.
1. Design
It all begins with a 3D drawing.
The client send us the CAD file of the boat hull and we prepare the file for production. Splitting the geometry up into production-sized panels - ensuring a perfect fit and minimum waste after thermoforming.
All production files of the core kit are sent to the client for approval prior to production.
2. Production
We prepare our flexible mould tooling for the thermoforming of the foam cores.
One by one, each 3D core panel is carefully shaped and cured. Inserts and chamfers are CNC machined and 3D printed, ensuring the highest precision possible.
After thermoforming, we label each 3D core kit panel according to a core-map of the entire boat hull design.
We carefully package the full 3D core kit for easy installation at the client site.
3. Installation
The client receives the 3D core kits on EPAL-pallet.
The core-map and a work instruction is provided to guide installation. Making the installation of the cores fast and easy.
Kurvatur also offers on-site installation support at an additional cost.
Interested in 3D Core kits ? Get in touch for a free weight-saving study.
